Just come to know about what is lean? If you are a management student or a super-efficient engineer, it is clear that you have landed on the right page to understand about what is Lean concept and to increase your understanding of that, Here, we are going to discuss all the lean concepts and its associated terms. Let us first start by understanding what does Lean manufacturing means here…
Lean concept extensively focuses only on one thing, Minimize waste to add mostly to the customer value, and Lean means to utilize the minimum or fewer resources with an ultimate aim to add value to customers. The organization which understands and adheres to the customer values always try to direct all its processes to increase the customer value.
The way to achieve this is focusing on Zero Waste, and this is a definite thing that if an organization focuses on the ultimate of zero waste, it can add excellent value to the customers, and to achieve zero waste, the organization direct all its efforts in this direction. In this effort, the organization tries to optimize all the assets, a flow of products/services, technologies both vertically and horizontally.
This effort helps the company to lessen the human struggles, decreasing the requirement of more space, time and capital for the production, and the indirect result of this is that the company becomes more efficient to respond and act quickly to the ever-changing customer desires and values.
With all the discussion above, let us summarize the Lean concept with these three basic critical concepts of Lean Process
- Lean Process in not only an event or process but a mindset.
- The efficiency with this concept can only be achieved when it is applied across all over the organization and not only to some specified areas.
- The lean process delivers faster and provides the best value to the consumers.
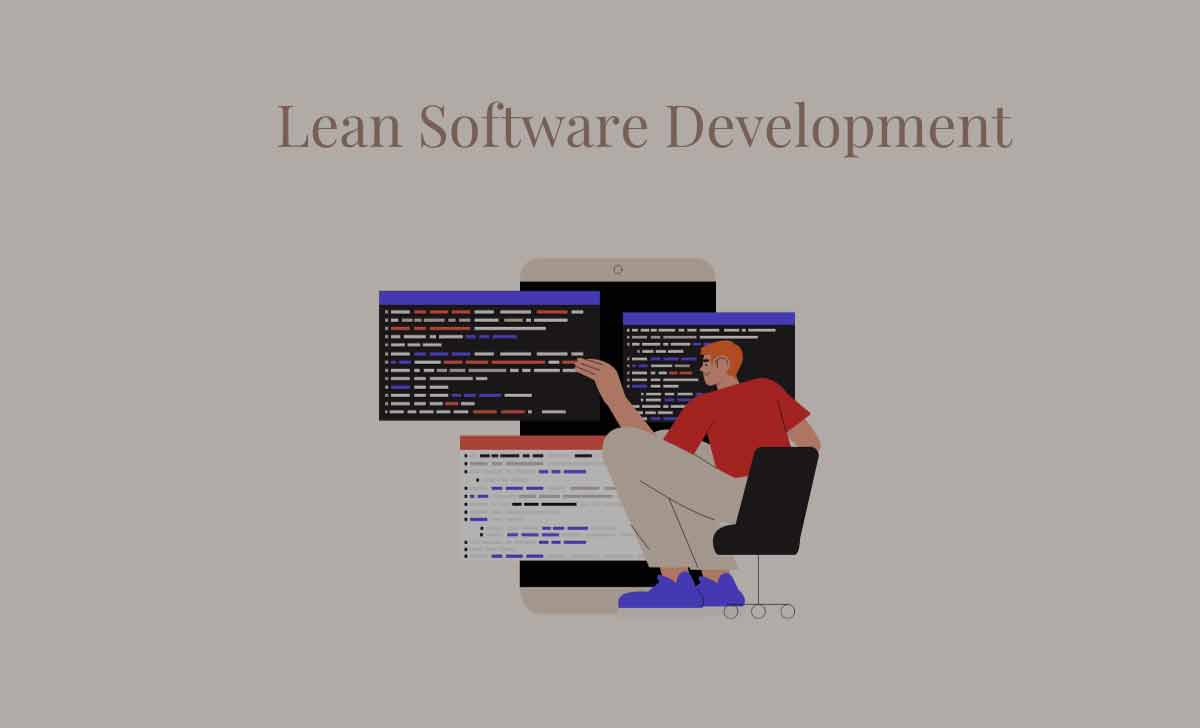
Is Lean Meant only for the Manufacturing
By all the discussion above, you must have got an idea that lean concept in meant only for the manufacturing but this is not so actually, and it applies to all types of business and processes. People with limited knowledge of concept view this is as a concept which gives a push to the cost reduction program in the organization.
However, they make a mistake there, and it is a way of thinking, It is a way to act for an entire organization with an aim to minimize any waste, be it an effort, time, space or money.
When some organization uses the term lean transformation, it means that they are indicating that they are moving their company with a new perspective and moving from the traditional/process bound thinking to lean thinking.
History of Lean
Initially, the term has Japanese origin, and it was coined in 1988 by John Krafcik, and the description of it was found in his article Triumph of the Lean Production System Krafick was a quality engineer in Toyota. Later, in 1990, James Womack defined the concept of lean in his book, The Machine that Changed the World.
There are two ways in which the concept of Lean was approached, the first, people identify it as a set of tools that helps to reduce the production of any waste. The most common tools used with this purpose are SMED, Five S, Poka-Yoke, Rank order clustering, control charts, etc.
The second is the Toyota Way, In this process, the focus is mainly on improving and increasing the smoothness of work by eliminating mura (unevenness) throughout the organization, and it is clear that this philosophy does not just focus on the waste reduction The tools used to achieve this are production leveling, Heinjunka box, pull production, etc.
It is clear that both the approaches use distinctive approach. The Toyota way is broadly defined as Toyota DNA. Four rules limit the Toyota DNA or TPS (Toyota Production System):
- The content, timing, and consequence of all the works must be highly specified.
- The supplier-customer connection must be direct.
- The pathway of the service or production must also be direct and simple.
- An improvement sought in the organization must follow any scientific method and must not be abrupt.
The learning aspects of the TPS have laid the foundation for the concept of lean.
Types of Wastes
Three types of waste are highly reduced by using lean technologies, and these are defined by the TPS model,
- Muda (a work that does not adds to any value)
- Muri (overburden)
- Mura (Unevenness)
Generally, the types of waste are
- Waiting: Waiting is a severe waste in an organization, and Waiting has many aspects attached to it. How much is the waiting time between different production steps? Is there an interdependence? Does someone or something have to wait for someone/something else?
- Inventory: Is the raw material is in excess? If it needs an extensive storage capacity and needs to be stored for a long time before it is being used?
- Over-processing: Does the work is inefficient, and you need to work on it over and over again?
- Over-production: Have you identified the correct amount of production value? Alternatively, if you are generating excessive amount and incur excessive storage costs?
- Transportation: How do you carry your material from one place to the other? Are you bringing it at the right price and with proper mode of transportation?
- Workforce: How are workers being used? Are they used efficiently? Do you utilize their full potential?
- Defects: Does there are any recurring defects? Time is taken to remove the defects after each cycle of production.
- Motion: how efficient is the movement of the people or equipment between different tasks.
Famous Principles of Lean Technology
There are five crucial principles outlined on which the lean concept works. Let us quickly go through them.
- Specify Value: It is necessary to specify the value from the customer standpoint. The work needs to be done by the product family.
- Identify/Create Value Streams: Identification of each step in the value stream of any product family is of utmost value. It ensures that there is no step taken where no value is produced.
- The flow of value towards the customer: Lean concept ensures that the value generation process adheres to a definite sequence to that the raw-material/product flows smoothly toward the customer.
- Pull Production: Instead of pushing the values, lean concepts lets the customer pull value. So no push but pull production should be ensured.
- Attain Perfection: When all the principle mentioned above is followed, again and again, the result is the state of perfection as value and value streams have already been identified, wasted steps are removed and pull strategy is in place.
Very Famous Lean Tools & Techniques
- 5S: This is an organized approach to housekeeping which reduces motion at a micro level, and it places the tools, objects and other parts at the optimum locations.
- Automation: This is a standard tool, as the name suggests, it monitors the automated machines with the help of ingenious devices, and this helps to stop the mechanisms when any problem occurs automatically.
- Continuous Flow: As the name suggests, this technique improves the product to move the product at a constant rate throughout the value stream.
- DFSS (Design of Six Sigma): This technique applies to the designing of products and their manufacturing process. Defectless manufacturing of the product is ensured by it.
- Elimination of Waste: This is the overreaching theme of the entire Lean manufacturing process. It improves the effectiveness by eliminating production of any waste.
- Focused Factories: Within a plant, this technique helps to segregate it in sections on the basis of markets or product lines. Overall, it aligns the process to match with the marketing strategies.
- In-Station Quality Control: This is a technique used to ensure that any product is defectless when it moves out of the workstation. SPC, routine inspection, poka-yoke, etc. are the most common techniques used to secure it.
- Jidoka: This is a practice to stop the production line in case workstation encounters a problem. Such a process creates a crisis like the atmosphere and demands the immediate solution.
- Kaizen: It is a technique used to make thing better in two ways: (a) By rapid improvement (Blitz) and (b) Slow Continuous Improvement.
- Kanban: This technique helps to schedule production. It establishes small stockpoint. When it is created, a small signal is sent showing that some items are withdrawn by some downstream process.
- Lean Accounting: This is a tool used to document lean savings. It includes activities like process costing, activity-based costing, etc. It accurately accounts all lean activities systematically.
- SDWT (Self Directed Work Teams): These teams manage the daily work. There is no formal leadership structure for these teams, but they operate the day-to-day work efficiently.
- SPC (Statistical Process Control): This is a tool/technique which establishes that a process is capable and at the same time it is controlled. It employs the statistical methods to do so.
- Total Quality Management (TQM): This is again a technique to improve process capability. TQM uses different SPC methods in unique combinations to ensure that no external factor can affect the process negatively or drives it out of control somehow.
- SMED: This technique analyzes the setup as a process, and to do so, it uses the conventional and works simplification techniques, where the result of this technique is that it makes the structure highly predictable and of high quality.
These are just a few techniques and tools, and there are many other tools as well that needs to be learned and employed for the success of any organization. So now you may know what is lean and for using the lean concept, one thing is always to be kept in mind, and it is to be used as a philosophy to inculcate the culture of lean, and only using the tools and techniques may sometimes not be able to produce appropriate and intended results.